Urarekiko erresistentzia eskasa, azalera irregularra, hauts eduki handia eta luzera irregularra?Uretako pentsuen ekoizpenean ohiko arazoak eta hobetzeko neurriak
Uretako pentsuen eguneroko ekoizpenean hainbat alderditako arazo batzuk topatu ditugu.Hona hemen denekin eztabaidatzeko adibide batzuk, honela:
1, Formula
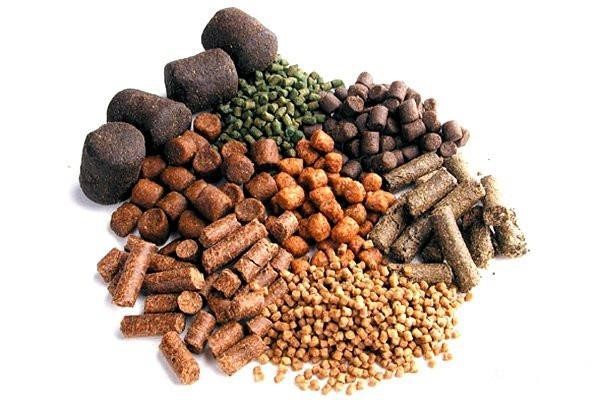
1. Arrainen pentsuaren formula-egituran, bazkariaren lehengai mota gehiago daude, hala nola koltza bazkaria, kotoi bazkaria, etab., zuntz gordinari dagozkionak.Olio-fabrika batzuek teknologia aurreratua dute, eta olioa, funtsean, lehorra frijitzen da oso eduki gutxirekin.Gainera, lehengai mota hauek ez dira erraz xurgatzen ekoizpenean, eta horrek eragin handia du granulazioan.Gainera, kotoizko bazkaria birrintzea zaila da eta horrek eraginkortasuna eragiten du.
2. Irtenbidea: koltza pastelaren erabilera areagotu egin da, eta kalitate handiko tokiko osagaiak gehitu zaizkio formulari, esate baterako, arroz branka.Gainera, formularen %5-8 inguru hartzen duen garia gehitu da.Doikuntzaren bidez, 2009an granulazio-efektua nahiko aproposa da, eta tonako etekina ere handitu da.2,5 mm-ko partikulak 8-9 tona artekoak dira, ia 2 tonako gehikuntza iraganarekin alderatuta.Partikulen itxura ere nabarmen hobetu da.
Horrez gain, kotoi-haziak birrintzeko eraginkortasuna hobetzeko, kotoi-haziak eta koltza bazkaria 2:1 proportzioan nahastu ditugu birrintzeko aurretik.Hobetu ondoren, birrintzeko abiadura, funtsean, koltza bazkariaren birrintze abiaduraren parekoa zen.
2, Partikulen gainazal irregularra
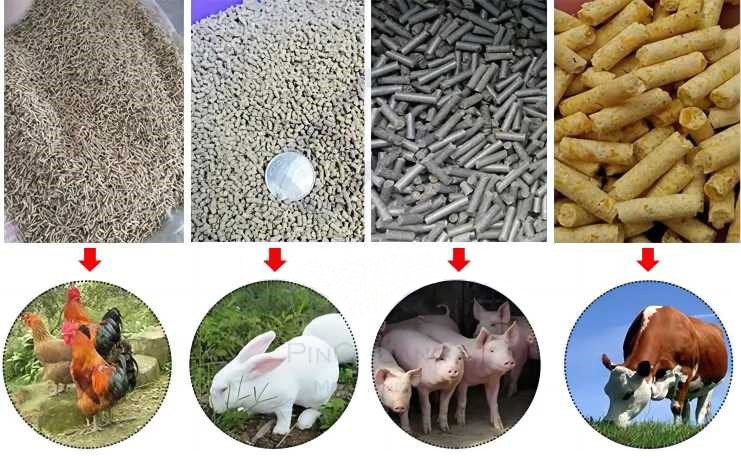
1. Amaitutako produktuaren itxuran eragin handia du, eta urari gehitzean, kolapsatzeko joera du eta erabilera-tasa baxua du.Arrazoi nagusia hau da:
(1) Lehengaiak lodiegi xehatzen dira, eta tenplaketa prozesuan zehar, ez dira guztiz heldu eta leuntzen, eta ezin dira ondo konbinatu beste lehengai batzuekin moldeko zuloetatik igarotzean.
(2) Zuntz gordinen eduki handia duen arrainen elikadura-formulan, tenplaketa-prozesuan lurrun-burbuilak daudenez, burbuila hauek apurtzen dira moldearen barruko eta kanpoaldeko presio-diferentziaren ondorioz partikulen konpresioan. partikulen azalera irregularra sortzen da.
2. Kudeaketa neurriak:
(1) Kontrolatu birrintze-prozesua behar bezala
Gaur egun, arrainen pentsuak ekoizten dituenean, gure enpresak 1,2 mm-ko bahe-mikro-hautsa erabiltzen du lehengai solte gisa.Bahearen erabilera-maiztasuna eta mailuaren higadura-maila kontrolatzen ditugu birrintzearen fintasuna bermatzeko.
(2) Kontrolatu lurrunaren presioa
Formularen arabera, doitu lurrunaren presioa zentzuz ekoizpenean, orokorrean 0,2 inguru kontrolatuz.Arrainen elikadura-formulan zuntz lodiko lehengai kopuru handia dela eta, kalitate handiko lurruna eta tenplaketa denbora egokia behar dira.
3, Partikulen urarekiko erresistentzia eskasa
1. Arazo mota hau gure eguneroko ekoizpenean ohikoena da, orokorrean faktore hauei lotuta:
(1) Tenplaketa-denbora laburrak eta tenperatura baxuak tenplaketa irregularra edo ez nahikoa, heltze-maila baxua eta hezetasun nahikoa eragiten dute.
(2) Material itsasgarri nahikorik ez izatea, hala nola almidoia.
(3) Eraztun-moldearen konpresio-erlazioa baxuegia da.
(4) Formulako olio-edukia eta zuntz gordinaren lehengaien proportzioa altuegiak dira.
(5) Birrintzeko partikulen tamainaren faktorea.
2. Kudeaketa neurriak:
(1) Hobetu lurrunaren kalitatea, egokitu erregulagailuaren pala angelua, tenplatzeko denbora luzatu eta lehengaien hezetasun-edukia egoki handitu.
(2) Egokitu formula, almidoizko lehengaiak egoki handitu eta gantz eta zuntz gordinaren lehengaien proportzioa murriztu.
(3) Gehitu itsasgarria behar izanez gero.(Sodio oinarritutako bentonita minda)
(4) Hobetu konpresio-erlazioaeraztun hil
(5) Kontrolatu ondo birrintzearen fintasuna
4, Hauts gehiegizko edukia partikuletan
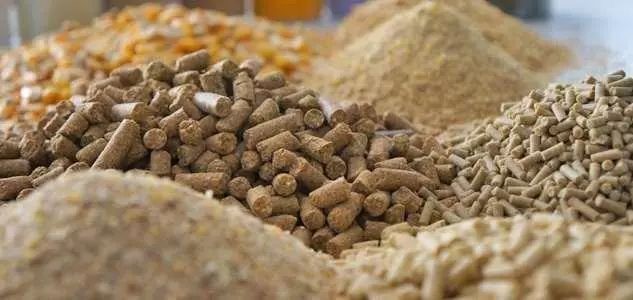
1. Zaila da pellet elikadura orokorraren itxura ziurtatzea hoztu ondoren eta pantailaratu aurretik.Bezeroek jakinarazi dute pelletetan errauts eta hauts fin gehiago daudela.Aurreko analisian oinarrituta, uste dut hainbat arrazoi daudela:
A. Partikulen gainazala ez da leuna, ebakia ez da txukuna eta partikulak solteak eta hautsa ekoizteko joera dute;
B. Pantaila kalifikatuz egindako baheketa osatu gabea, pantaila-sare blobatua, gomazko bolen higadura larria, pantaila-sarearen irekidura desegokia, etab.
C. Amaitutako produktuen biltegian errauts fin asko dago, eta garbiketa ez da sakona;
D. Ezkutuko arriskuak daude hautsa kentzean ontziratzean eta pisatzean;
Kudeaketa neurriak:
A. Optimizatu formula-egitura, hautatu eraztun-troketa zentzuz eta ondo kontrolatu konpresio-erlazioa.
B. Granulazio-prozesuan zehar, kontrolatu tenplaketa-denbora, elikadura-kopurua eta granulazio-tenperatura lehengaiak guztiz heldu eta leuntzeko.
C. Ziurtatu partikulen sekzioa txukuna dela eta erabili altzairuzko zerrendaz egindako ebakitzeko labana leun bat.
D. Egokitu eta mantendu kalifikazio-pantaila, eta erabili arrazoizko pantaila-konfigurazioa.
E. Amaitutako produktuen biltegiaren azpian bigarren mailako pantaila-teknologia erabiltzeak hautsaren edukiaren ratioa asko murrizten du.
F. Beharrezkoa da amaitutako produktuen biltegia eta zirkuitua garaiz garbitzea.Horrez gain, ontziratzea eta hautsa kentzeko gailua hobetu behar da.Hobe da presio negatiboa erabiltzea hautsa kentzeko, hau da, idealagoa.Batez ere ontziratzeko prozesuan, ontziratzeko langileak aldian-aldian kolpatu eta garbitu behar du hautsa ontzi-eskalaren buffer-hoppertik..
5, Partikulen luzera aldatu egiten da
1. Eguneroko ekoizpenean, askotan kontrolean zailtasunak aurkitzen ditugu, batez ere 420tik gorako ereduetan. Honen arrazoiak gutxi gorabehera honela laburbiltzen dira:
(1) Granulaziorako elikadura-kopurua irregularra da, eta tenplaketa-efektua asko aldatzen da.
(2) Moldearen arrabolen arteko tarte ez-koherentea edo eraztun-moldearen eta presio-arrabolen higadura larria.
(3) Eraztun-moldearen norabide axialean zehar, bi muturretako deskarga-abiadura erdian dagoena baino txikiagoa da.
(4) Eraztun-moldearen presioa murrizteko zuloa handiegia da eta irekitze-tasa altuegia da.
(5) Ebaketa-orriaren posizioa eta angelua zentzugabeak dira.
(6) Granulazio-tenperatura.
(7) Eraztun-ebakitzeko xaflaren motak eta altuera eraginkorrak (xaflaren zabalera, zabalera) eragina dute.
(8) Aldi berean, konpresio-ganberaren barruan lehengaien banaketa irregularra da.
2. Pentsuen eta pelleten kalitatea, oro har, barneko eta kanpoko kualitateen arabera aztertzen da.Ekoizpen-sistema gisa, pentsu-pelleten kanpo-kalitatearekin zerikusia duten gauzetara hurbiltzen gara.Ekoizpenaren ikuspegitik, uretako pentsuen pelletaren kalitatean eragiten duten faktoreak gutxi gorabehera honela laburbil daitezke:
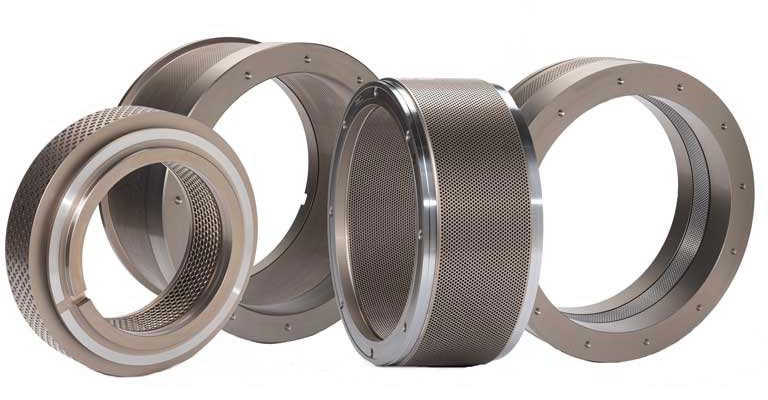
(1) Formulen diseinuak eta antolakuntzak eragin zuzena dute uretako pentsu-pelleten kalitatean, guztizkoaren %40 gutxi gorabehera;
(2) Birrintzearen intentsitatea eta partikulen tamainaren uniformetasuna;
(3) Eraztun moldearen diametroak, konpresio-erlazioak eta abiadura linealak eragina dute partikulen luzera eta diametroan;
(4) Eraztun-moldearen konpresio-erlazioa, abiadura lineala, itzaltze- eta tenplaketa-efektua eta ebaketa-xaflaren eragina partikulen luzeran;
(5) Lehengaien hezetasun edukiak, tenplaketa efektuak, hozteak eta lehortzeak eragina dute produktu bukatuen hezetasun edukian eta itxuran;
(6) Ekipamenduak berak, prozesu-faktoreek eta itzaltze- eta tenplatze-efektuek eragina dute partikulen hautsaren edukian;
3. Kudeaketa neurriak:
(1) Egokitu oihal-arraskaren luzera, zabalera eta angelua, eta ordezkatu gastatutako arraspa.
(2) Erreparatu ebaketa-xaflaren posizioa egokitzea ekoizpenaren hasieran eta amaieran, elikadura-kopuru txikia dela eta.
(3) Ekoizpen prozesuan, ziurtatu elikadura-tasa egonkorra eta lurrun-hornidura.Lurrunaren presioa baxua bada eta tenperatura ezin bada igo, behar bezala egokitu edo gelditu behar da.
(4) Arrazoiz egokitu arteko tartearoller shell.Jarraitu molde berria arrabol berriekin, eta berehala konpondu presio-arrabolaren eta eraztun-moldearen azalera irregularra higadura dela eta.
(5) Konpondu eraztun-moldearen gida-zuloa eta berehala garbitu blokeatutako molde-zuloa.
(6) Eraztun-moldea eskatzerakoan, jatorrizko eraztun-moldearen norabide axialaren bi muturretako hiru zulo-lerroen konpresio-erlazioa erdian dagoena baino 1-2 mm txikiagoa izan daiteke.
(7) Erabili ebaketa-labana leun bat, 0,5-1mm arteko lodiera kontrolatua duena, ertz zorrotza ahalik eta gehien ziurtatzeko, eraztun-moldearen eta presio-arrabolaren arteko sare-lerroan egon dadin.
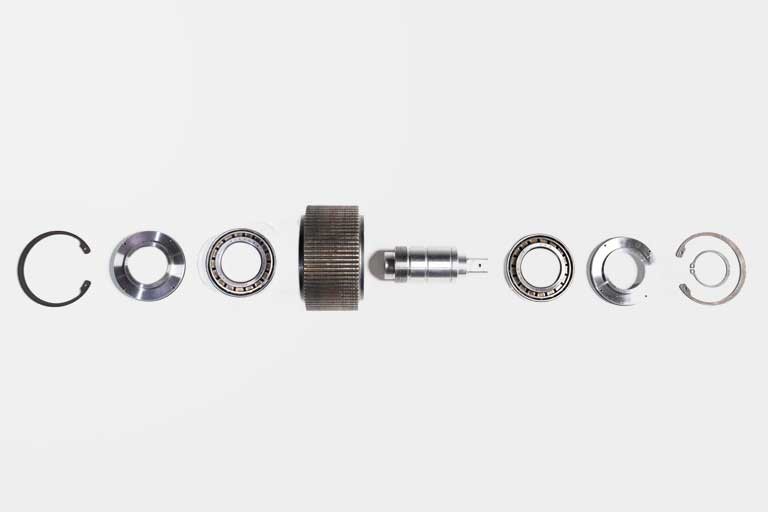
(8) Ziurtatu eraztun-moldearen kontzentrikotasuna, egiaztatu aldian-aldian granulagailuaren ardatzaren sakea eta egokitu behar izanez gero.
6, Laburpena Kontrol puntuak:
1. Artezketa: Artezteko fintasuna zehaztapen-baldintzen arabera kontrolatu behar da
2. Nahasketa: lehengaien nahastearen uniformetasuna kontrolatu behar da nahasketa kopuru egokia, nahasketa denbora, hezetasun edukia eta tenperatura ziurtatzeko.
3. Heltzea: puzteko makinaren presioa, tenperatura eta hezetasuna kontrolatu behar dira
Partikula-materialaren tamaina eta forma: konpresio-moldeen eta ebaketa-laben zehaztapen egokiak hautatu behar dira.
5. Amaitutako pentsuaren ur edukia: beharrezkoa da lehortzeko eta hozteko denbora eta tenperatura ziurtatzea.
6. Olio-ihinztatzea: beharrezkoa da olio-ihinztatze-kopuru zehatza, tobera kopurua eta olioaren kalitatea kontrolatzea.
7. Baheketa: bahearen tamaina hautatzea materialaren zehaztapenen arabera.
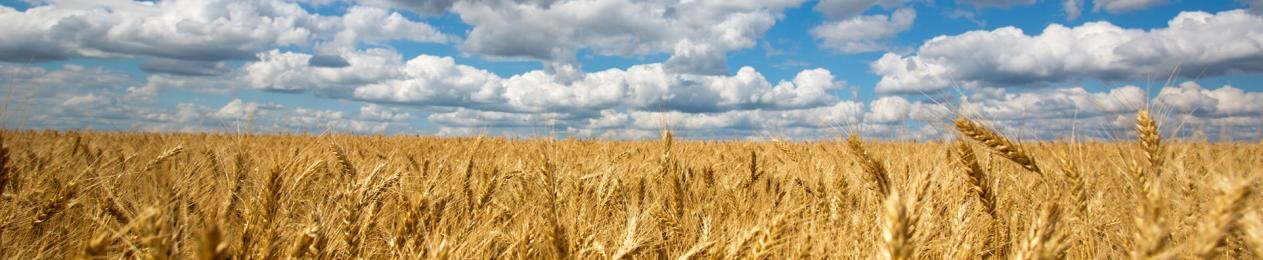
Argitalpenaren ordua: 2023-11-30