Urarekiko erresistentzia eskasa, gainazal irregularra, hauts-eduki handia eta luzera irregularra? Arazo ohikoenak eta hobekuntza-neurriak uretako pentsuen ekoizpenean
Gure eguneroko ur-elikagaien ekoizpenean, hainbat alderditatik datozen arazo batzuk aurkitu ditugu. Hona hemen guztiekin eztabaidatzeko adibide batzuk:
1. Formula
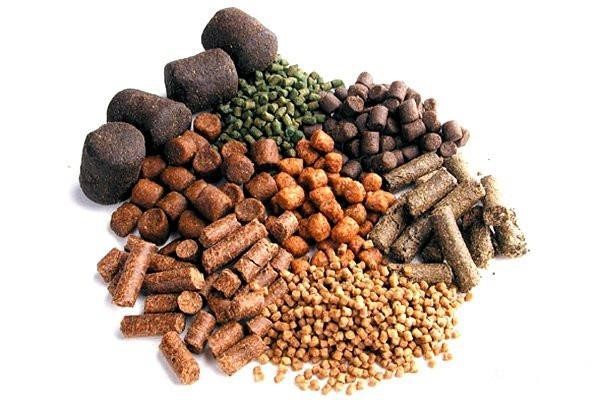
1. Arrain-pentsuen formula-egituran, zuntz gordinaren barruan, lehengai mota gehiago daude, hala nola koltza-irina, kotoi-irina, etab. Olio-fabrika batzuek teknologia aurreratua dute, eta olioa, funtsean, lehortu egiten da, edukiera oso txikiarekin. Gainera, lehengai mota hauek ez dira erraz xurgatzen ekoizpenean, eta horrek eragin handia du granulazioan. Horrez gain, kotoi-irina zaila da xehatzen, eta horrek eraginkortasunari eragiten dio.
2. Irtenbidea: Kolza-opilaren erabilera handitu da, eta kalitate handiko tokiko osagaiak gehitu zaizkio formulan, hala nola arroz-zahia. Horrez gain, garia gehitu da, formularen % 5-8 inguru osatzen duena. Doikuntzaren bidez, 2009ko pikortze-efektua nahiko aproposa da, eta tona bakoitzeko etekina ere handitu da. 2,5 mm-ko partikulak 8-9 tona artekoak dira, ia 2 tona gehiago iraganarekin alderatuta. Partikulen itxura ere nabarmen hobetu da.
Gainera, kotoi-irina xehatzeko eraginkortasuna hobetzeko, kotoi-irina eta koltza-irina 2:1 proportzioan nahastu genituen xehatu aurretik. Hobekuntzaren ondoren, xehatzeko abiadura, funtsean, koltza-irinaren xehatzeko abiaduraren parekoa zen.
2. Partikulen gainazal irregularra
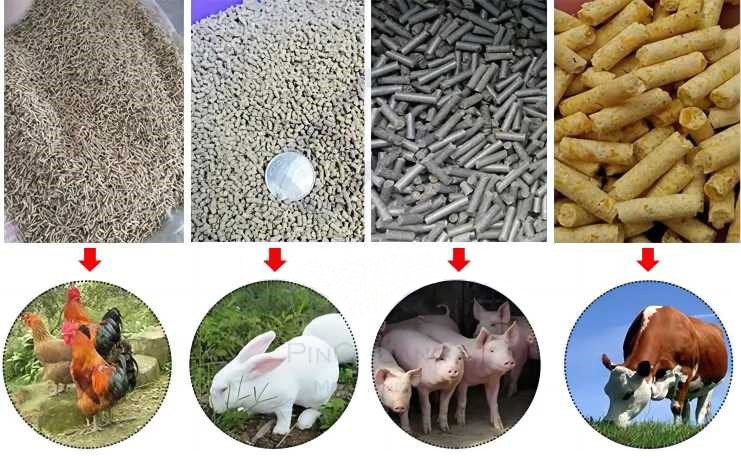
1. Eragin handia du produktu amaituaren itxuran, eta urari gehitzen zaionean, erortzeko joera du eta erabilera-tasa baxua du. Arrazoi nagusia hau da:
(1) Lehengaiak gehiegi xehatzen dira, eta tenplatze-prozesuan ez dira guztiz heldu eta bigundu, eta ezin dira ondo konbinatu beste lehengaiekin molde-zuloetatik igarotzean.
(2) Zuntz gordin asko duen arrain-pentsu formulan, tenplatze-prozesuan lehengaian lurrun-burbuilak daudenez, burbuila horiek lehertu egiten dira partikulen konpresioan zehar moldearen barrualdearen eta kanpoaldearen arteko presio-diferentziaren ondorioz, eta horrek partikulen gainazal irregularra sortzen du.
2. Kudeaketa neurriak:
(1) Birrintze-prozesua behar bezala kontrolatu
Gaur egun, arrain-pentsua ekoizteko, gure enpresak 1,2 mm-ko bahe-mikro-hautsa erabiltzen du lehengai gisa. Bahearen erabilera-maiztasuna eta mailuaren higadura-maila kontrolatzen ditugu xehaketaren fintasuna bermatzeko.
(2) Lurrun-presioa kontrolatu
Formularen arabera, lurrun-presioa arrazoiz doitu behar da ekoizpenean zehar, oro har 0,2 inguruan kontrolatuz. Arrain-pentsuaren formulan zuntz lodiko lehengai kopuru handia dagoenez, kalitate handiko lurruna eta tenplatze-denbora arrazoizkoa behar dira.
3. Partikulen urarekiko erresistentzia eskasa
1. Arazo mota hau da gure eguneroko ekoizpenean ohikoena, oro har, faktore hauekin lotuta:
(1) Tenplatzeko denbora laburrak eta tenplatzeko tenperatura baxuak tenplatze irregularra edo nahikoa ez izatea, heltze-maila baxua eta hezetasun nahikorik ez izatea eragiten dute.
(2) Almidoia bezalako itsasgarri-material nahikorik ez.
(3) Eraztun-moldearen konpresio-erlazioa baxuegia da.
(4) Formulako olio-edukia eta zuntz gordinaren lehengaien proportzioa altuegiak dira.
(5) Birrintzeko partikulen tamainaren faktorea.
2. Kudeaketa neurriak:
(1) Lurrunaren kalitatea hobetu, erregulatzailearen pala-angelua egokitu, tenplatze-denbora luzatu eta lehengaien hezetasun-edukia behar bezala handitu.
(2) Egokitu formula, handitu almidoi lehengaiak behar bezala, eta murriztu gantz eta zuntz gordinaren lehengaien proportzioa.
(3) Gehitu itsasgarria beharrezkoa bada. (Sodio oinarritutako bentonita-nahasketa)
(4) Hobetu konpresio-erlazioaeraztun-trokel
(5) Birrintzearen finura ondo kontrolatu
4. Partikuletan hauts gehiegi edukitzea
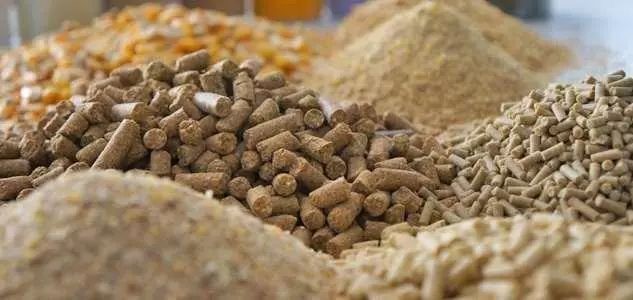
1. Zaila da pellet-elikadura orokorraren itxura ziurtatzea hoztu ondoren eta bahetu aurretik. Bezeroek jakinarazi dute errauts eta hauts fin gehiago daudela pelletetan. Goiko analisian oinarrituta, uste dut hainbat arrazoi daudela horretarako:
A. Partikulen gainazala ez da leuna, ebakidura ez da txukuna, eta partikulak solteak dira eta hautsa sortzeko joera dute;
B. Baheketa osatu gabea bahetze mailakatuz, bahe-sare buxatua, gomazko bolen higadura larria, bahe-sarearen irekidura desegokia, etab.
C. Errauts fin asko dago produktu amaituen biltegian, eta garbiketa ez da osoa egiten;
D. Ontziratzean eta pisatzean hautsa kentzean ezkutuko arriskuak daude;
Kudeaketa neurriak:
A. Formularen egitura optimizatu, eraztun-trokel egokia aukeratu eta konpresio-erlazioa ondo kontrolatu.
B. Granulazio prozesuan zehar, kontrolatu tenplatze denbora, elikadura kantitatea eta granulazio tenperatura lehengaiak guztiz heltzeko eta biguntzeko.
C. Ziurtatu partikulen zeharkako sekzioa txukuna dela eta erabili altzairuzko zerrendaz egindako ebakitzeko aizto bigun bat.
D. Kalifikazio-pantaila doitu eta mantendu, eta pantaila-konfigurazio arrazoizkoa erabili.
E. Bigarren mailako bahetze-teknologia erabiltzeak produktu amaituen biltegiaren azpian hauts-edukiaren erlazioa asko murriztu dezake.
F. Beharrezkoa da produktu amaituen biltegia eta zirkuitua garaiz garbitzea. Horrez gain, ontziratzea eta hautsa kentzeko gailua hobetzea beharrezkoa da. Hobe da hautsa kentzeko presio negatiboa erabiltzea, hau aproposagoa baita. Batez ere ontziratze prozesuan, ontziratzen duen langileak aldizka jo eta hautsa garbitu behar du ontziratze-balantzaren buffer-tolbatik..
5. Partikulen luzera aldatu egiten da
1. Eguneroko ekoizpenean, askotan zailtasunak izaten ditugu kontrolean, batez ere 420tik gorako modeloetan. Horren arrazoiak, gutxi gorabehera, honela laburbiltzen dira:
(1) Granulaziorako elikadura-kopurua ez da uniformea, eta tenplatze-efektua asko aldatzen da.
(2) Molde-arrabolen arteko tarte ez-koherentea edo eraztun-moldearen eta presio-arrabolen higadura larria.
(3) Eraztun-moldearen ardatz-norabidean zehar, bi muturretan isurketa-abiadura erdian baino txikiagoa da.
(4) Eraztun-moldearen presioa murrizteko zuloa handiegia da, eta irekitze-tasa altuegia.
(5) Ebaketa-xaflaren posizioa eta angelua ez dira arrazoizkoak.
(6) Granulazioaren tenperatura.
(7) Eraztun-trokelaren ebaketa-xaflaren motak eta altuera eraginkorrak (xaflaren zabalera, zabalera) eragina dute.
(8) Aldi berean, lehengaien banaketa ez da uniformea konpresio-ganberaren barruan.
2. Pentsuaren eta pelleten kalitatea, oro har, barne eta kanpo ezaugarrien arabera aztertzen da. Ekoizpen sistema gisa, pentsu pelleten kanpoko kalitatearekin lotutako gauzekiko eragin handiagoa dugu. Ekoizpenaren ikuspegitik, uretako pentsu pelleten kalitatean eragina duten faktoreak honela laburbil daitezke:
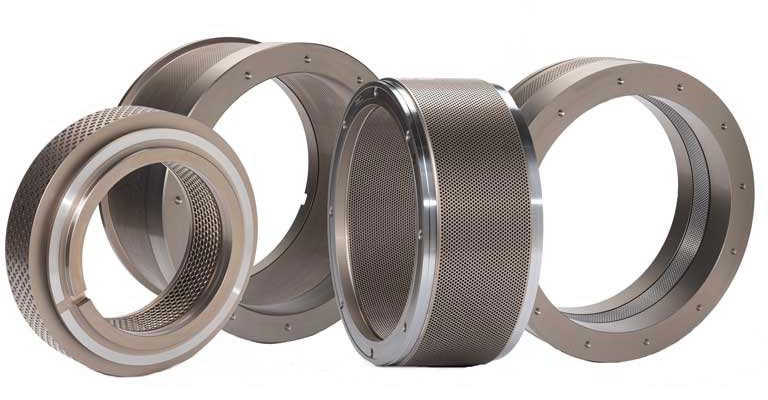
(1) Formulen diseinuak eta antolaketak eragin zuzena dute uretako pentsu-pelleten kalitatean, guztizkoaren % 40 inguru osatzen baitute;
(2) Birrintzearen intentsitatea eta partikulen tamainaren uniformetasuna;
(3) Eraztun-moldearen diametroak, konpresio-erlazioak eta abiadura linealak eragina dute partikulen luzeran eta diametroan;
(4) Eraztun-moldearen konpresio-erlazioa, abiadura lineala, hozte- eta tenplatze-efektua eta ebaketa-xaflak partikulen luzeran duen eragina;
(5) Lehengaien hezetasun-edukiak, tenplatze-efektuak, hozteak eta lehortzeak eragina dute produktu amaituen hezetasun-edukian eta itxuran;
(6) Ekipamenduak berak, prozesuaren faktoreek eta hozte eta tenplatze efektuek eragina dute partikula hauts edukian;
3. Kudeaketa neurriak:
(1) Oihal-arraskagailuaren luzera, zabalera eta angelua doitu, eta higatutako arraskagailua ordezkatu.
(2) Ekoizpenaren hasieran eta amaieran ebaketa-xaflaren posizioa garaiz doitzeari erreparatu, elikadura-kantitate txikia dela eta.
(3) Ekoizpen prozesuan zehar, ziurtatu elikatze-tasa eta lurrun-hornikuntza egonkorrak direla. Lurrun-presioa baxua bada eta tenperatura ezin bada igo, garaiz egokitu edo gelditu egin behar da.
(4) Arrazoiz egokitu arteko tarteagurpil-oskolaMolde berriaren ondoren, jarri arrabol berriak, eta konpondu berehala higaduragatik sortutako presio-arrabolaren eta eraztun-moldearen gainazal irregularra.
(5) Konpondu eraztun-moldearen gida-zuloa eta garbitu berehala blokeatutako molde-zuloa.
(6) Eraztun-moldea eskatzerakoan, jatorrizko eraztun-moldearen ardatz-norabidearen bi muturretan dauden hiru zulo-lerroen konpresio-erlazioa erdikoarena baino 1-2 mm txikiagoa izan daiteke.
(7) Erabili ebaketa-labana bigun bat, 0,5-1 mm arteko lodiera kontrolatukoa, ertz zorrotzena ahalik eta gehien ziurtatzeko, eraztun-moldearen eta presio-arrabola arteko engranaje-lerroan egon dadin.
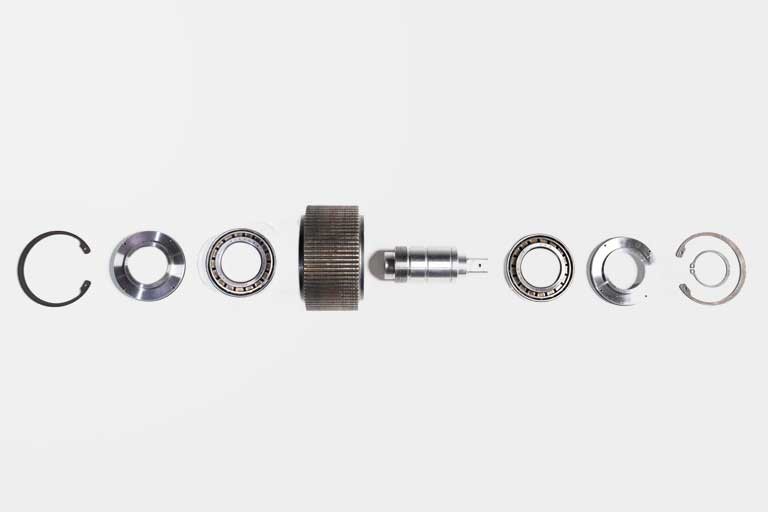
(8) Ziurtatu eraztun-moldearen zentrokidetasuna, egiaztatu aldizka granulatzailearen ardatzaren tartea eta doitu behar izanez gero.
6. Kontrol puntuen laburpena:
1. Ehotzea: Ehotzearen finura zehaztapen-eskakizunen arabera kontrolatu behar da
2. Nahasketa: Lehengaien nahasketaren uniformetasuna kontrolatu behar da nahasketa-kantitate, nahasketa-denbora, hezetasun-edukia eta tenperatura egokiak direla ziurtatzeko.
3. Heltzea: Puzteko makinaren presioa, tenperatura eta hezetasuna kontrolatu behar dira
Partikula-materialaren tamaina eta forma: konpresio-moldeen eta ebaketa-xaflen zehaztapen egokiak aukeratu behar dira.
5. Amaitutako pentsuaren ur-edukia: lehortzeko eta hozteko denbora eta tenperatura bermatu behar dira.
6. Olio-ihinztadura: Olio-ihinztaduraren kantitate zehatza, toberen kopurua eta olioaren kalitatea kontrolatu behar dira.
7. Bahetzea: Aukeratu bahearen tamaina materialaren zehaztapenen arabera.
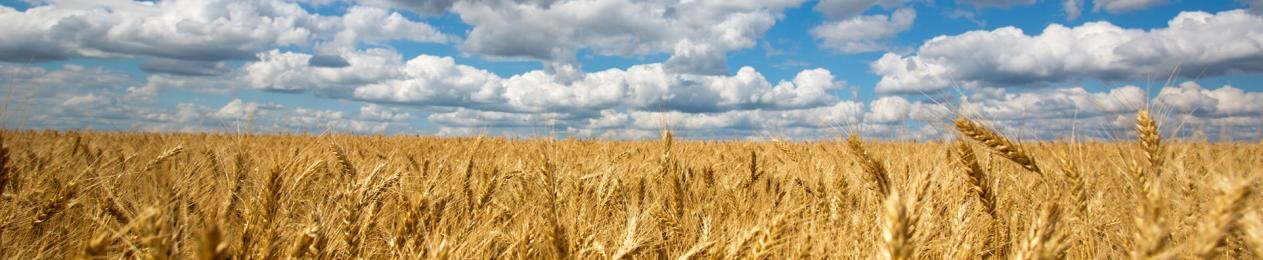
Argitaratze data: 2023ko azaroaren 30a